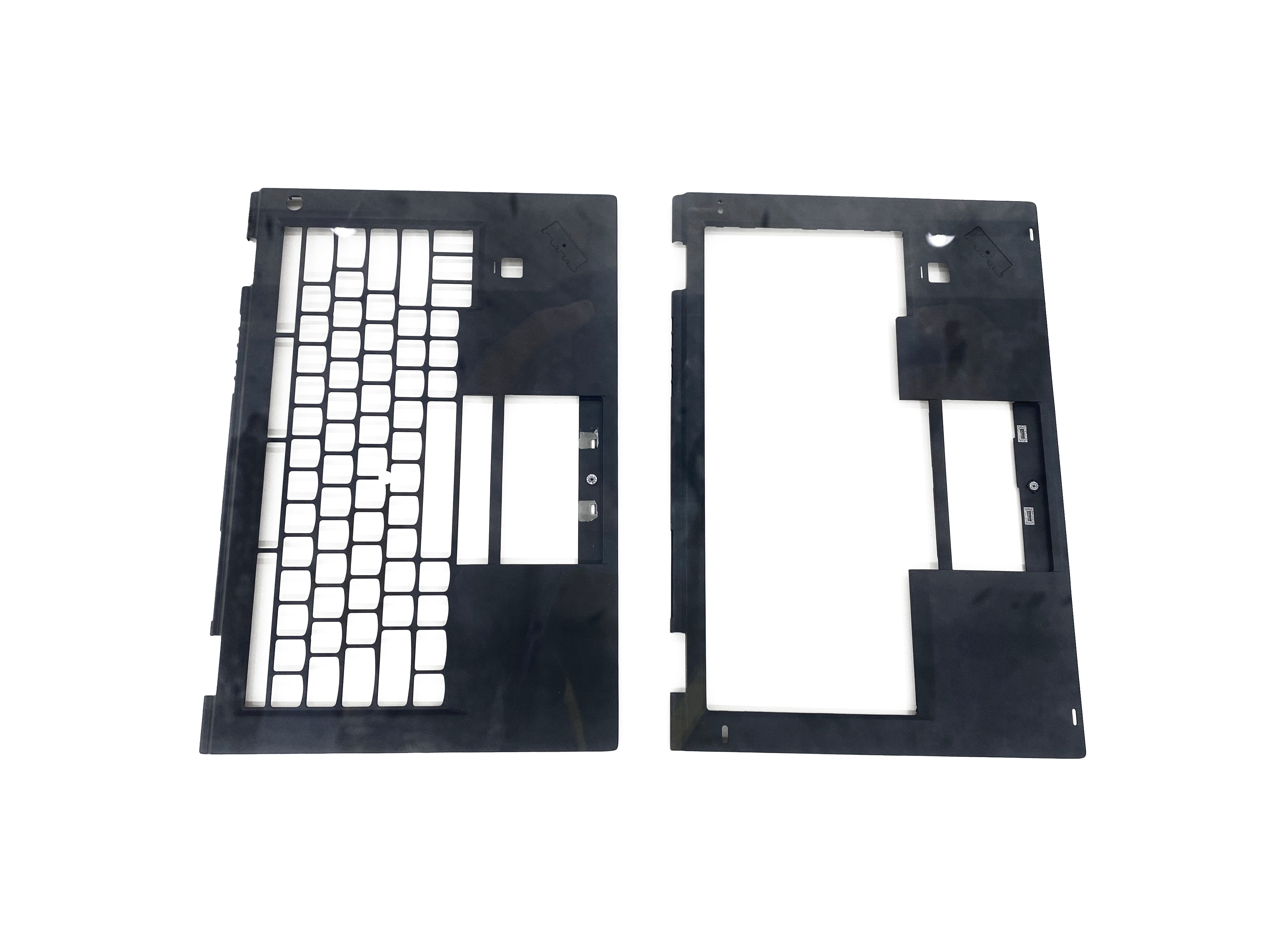
Magnesium alloy smelting operation and safe production
Since the magnesium alloy liquid is easily oxidized, the oxide film formed on the surface is loose, and the density coefficient α is only 0.79, which does not prevent the alloy from continuing to oxidize. The magnesium alloy liquid reacts with oxygen, water vapor and nitrogen in the atmosphere to form refractory magnesium oxide, Mg3N2 and other compounds that are not melted in the magnesium liquid, and mixed with the mold to form "oxide slag". Therefore, it is very important to prevent oxidation when melting the alloy. There are two main methods of magnesium alloy melt protection, namely flux and gas protection.
Melting with protective flux usually brings the following problems:
- Chloride and fluoride salts volatilize at high temperature, producing toxic gases such as HCl, Cl2, HF;
- Due to the high density of flux, some flux may accompany The magnesium liquid is mixed into the mold, causing "flux slag";
- The gas generated by the volatilization of the flux may penetrate into the alloy liquid and become a source of corrosion during the use of the material, accelerating the corrosion of the material and reducing the service life.
Currently, most manufacturers use gas shielding, that is, use a mixture of two or four dry SF6, N2, CO2, and SO2 gases to form a dense continuous film on the surface of the magnesium alloy bath to prevent oxidation of the magnesium alloy liquid. SF6 is not a toxic gas, but its greenhouse effect on the earth is 24,000 times that of carbon dioxide, and the magnesium industry's SF6 dose accounts for 7% of the world's total use (1996). In the future, it will inevitably limit its use or even stop using it, but it has not yet found a suitable replacement for SF6. Studies have shown that SO2 formed by spraying sulfur powder on the surface of the molten pool has a protective effect on the magnesium alloy solution.
For die-casting magnesium alloys, the main researches are as follows:
- High temperature performance: At present, AZ and AM series magnesium alloy die castings account for 90% of magnesium alloy castings for automobiles. The strength of the magnesium alloy series decreases significantly above 150°C. An AS series die-cast magnesium alloy with creep resistance above 150°c has been developed, such as AS41A alloy (Mg43 aluminum 1% Si 0.35 Mn), its creep strength at 175°c is better than AZ91D and AM60B, and has a higher creep strength than AZ91D and AM60B. High elongation, yield strength and tensile strength. day. Volkswagen Beetle engine crankcases have been using AS41 and AS42, and the recently adopted improved alloy AE42 has better creep properties at high temperatures. The rare earth elements Y, Nd, Sr and other trace elements have a significant grain refinement effect on die-casting magnesium alloys, which can improve the strength and creep resistance of die-casting magnesium alloys. For example, the recently developed AE42 has better creep resistance than traditional MgAlSi alloys for long-term use at 200-250 °C. However, the improvement in high temperature performance of AS and Aehejin is still limited. Its casting performance is poorer than that of AZ and AE alloys, and the high cost of rare earth elements limits its production and application.
- Ductility: Currently, magnesium die castings grow very rapidly and are suitable for applications requiring safety and high fracture toughness. To improve the ability to absorb energy, the fracture toughness of the material should be improved. This can be achieved by reducing the aluminium in the alloy. AM60 and AM50 are widely used in safety components such as dashboard brackets, steering wheels and seats. AM20 is also currently used in the rear frame of the seat. In addition, the elongation at break is also quite closely related to temperature, especially above 50 °C, which increases with increasing temperature.
- Magnesium alloy matrix composites: Magnesium alloy matrix composite reinforcement particles, such as silicon carbide, have been researched and developed for many years, although they have not yet reached the stage of commercial application in die casting. However, castings such as impellers, bicycle cranks, and automobile cylinder liners are all manufactured by sand casting and precision casting methods, and this composite material has been combined with semi-solid casting for the development of die casting.
Conclusion
For more information about die casting cost,die casting material,hot chamber die casting process, we are glad to answer for you.